All about Manufacturings
Wiki Article
Some Of Plastic Manufacturing
Table of ContentsNot known Details About Lean Manufacturing A Biased View of Die CastingLean Production Can Be Fun For EveryoneSome Known Incorrect Statements About Mfg What Does Plastic Manufacturing Mean?Little Known Questions About Manufacturing Industries.
The message on this page is an example from our complete White Paper 'Injection Moulding for Customers' - * Example text * - for full guide click the download button above! Intro This overview is intended for individuals who are looking to source plastic mouldings. It offers a much needed understanding right into all that is included with producing plastic parts, from the mould device needed to the moulding procedure itself.If you desire to explore even more, the guide covers kinds of mould tools, along with unique ending up processes such as colours & plating. Words that are underlined can be discovered in the reference in the appendix ... Part I: Moulding: The Essentials The Advantages of Injection Moulding Plastic injection moulding is a very accurate procedure that provides a number of advantages over various other plastic handling approaches.
Accuracy is best for very elaborate components. You can hold this moulding in the hand of your hand and also it has employers, ribs, steel inserts, side cores and holes, made with a sliding shut off feature in the mould device.
All about Mfg
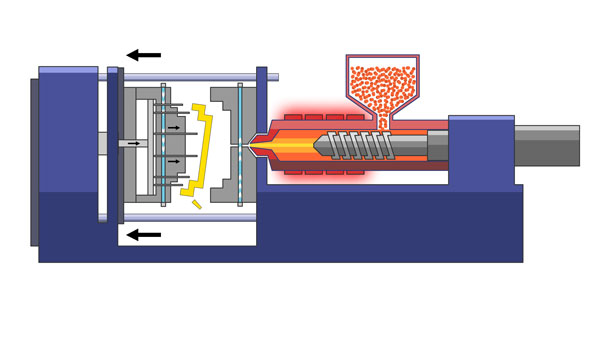

from material feed & melting; product injection; cooling time as well as ejection to the re-closing of the mould device ready for the following cycle. Draft angles - The walls of a moulded component must be somewhat tapered in the direction in which the component is ejected from the mould device, to allow the part to be expelled conveniently.
Ejector stroke - The pressing out of ejector pins to eject the moulded part from the mould tool. Ejector stroke speed, length and timing requires to be carefully regulated to stop damage to the ejectors as well as mould tool, but at the exact same time make the moulding cycle as brief as feasible.

The Basic Principles Of Manufacturing
Ribs - When a plastic part has slim walls, ribs are contributed to the design to make the thin wall surfaces more powerful Side cores - Side action which creates a function on a moulded part, at an opposing angle to the regular opening direction of the mould device. additive manufacturing. The side core requires to be able to withdraw as the plastic component can not be ejected otherwise.
Walls - The sides of a moulded component The message on this page is an example from our complete White Paper 'Shot Moulding for Customers'.
Injection moulding is commonly used for manufacturing a variety of parts, from the smallest parts to entire body panels of automobiles. Injection moulding uses a special-purpose equipment that has 3 parts: the shot device, the mould and the clamp.
Die Casting Things To Know Before You Get This
Process characteristics [edit] Shot moulding uses a ram or screw-type plunger to require liquified plastic or rubber product into a mould cavity; this strengthens right into a form that has actually satisfied the contour of the mould. It is Check This Out most frequently used to process both thermoplastic as well as thermosetting polymers, with the volume used of the previous being significantly higher.: 13 Thermoplastics are prevalent as a result of attributes that make them very ideal for shot moulding, such as convenience of recycling, convenience for a variety of applications,: 89 and ability to soften as well as stream on heating.In several tooth cavity moulds, each cavity can be similar and form the exact same components or can be special and form several various geometries throughout a single cycle. Moulds are normally made from tool steels, however stainless-steels as well as aluminium moulds are ideal for particular applications. Aluminium moulds are generally ill-suited for high quantity production or components with narrow dimensional resistances, as they have substandard mechanical homes and also are more vulnerable to use, damage, and contortion throughout the shot and clamping cycles; nevertheless, aluminium moulds are cost-effective in low-volume applications, as mould fabrication prices as well as time are significantly minimized.
When sufficient product has actually collected, the material is compelled at high pressure and also rate into the part forming tooth cavity. The specific quantity of shrinkage is a feature of the resin being used, and can be fairly foreseeable. To stop spikes in stress, the procedure usually utilizes a transfer setting matching to a 9598% complete dental caries where the screw changes from a consistent rate to a constant pressure control.
About Lean Manufacturing
The packaging pressure is applied up until the gate (dental caries entryway) strengthens. Due to its small size, the gate is usually the initial area to solidify via its entire thickness.: 16 Once the gate solidifies, no even more material can get in the tooth cavity; accordingly, look at more info the screw reciprocates and also obtains material for the following cycle while the product within the mould cools so that it can be expelled as well as be dimensionally secure.Report this wiki page